Le Calmacro
Par Francis, le 31 Aout 2008
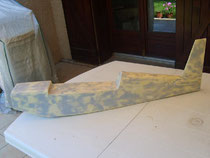
Le Master fait de ploystyrene extrudé recouvert de tissus de verre + résine epoxi.
Mastiqué , poncé , vernis et poli .
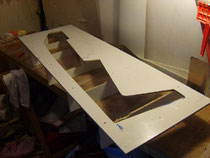
Plan de joint en mélaminé lisse de préférence .
Epaisseur 10mm .
Monté sur traverses servant de berceau au master.
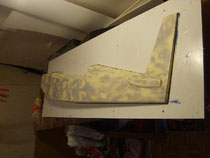
Le master en place dans le plan de joint .
Le raccord entre le plan de joint et le master a été fait avec de la plastiline .
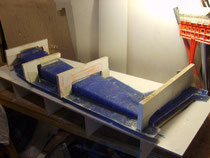
Le master recouvert de la stratification avec ses pieds .
La couleur bleue est due à la couleur du gelcot fait par mes soins.
Résine polyesther +colorant+fibre de coton +aerosil .
La stratification est faite avec du mat de verre et de la résine polyesther .
Une couche de voile +2 couches de 250g +une couche de 450g et de nouveau un voile .
Le pieds sont colés à la résine avec refort de tissu . Voir plus loin .
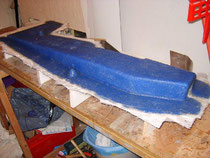
La première partie du moule avec le master a l'intérieur a été retiré du plan de joint
, retouné (voir avant dernière photo) et la deuxième partie du moule a été stratifiée.
Je passe sur les détails de cirage et de mise en place des détrompeurs centreurs que l'on peut apercevoir sur le bord .
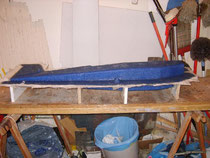
Le même vu sous un autre angle .
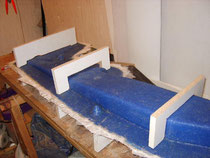
Mise en place des pieds.
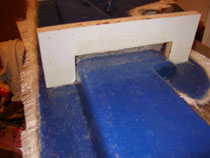
Detail du collage des pieds . On voit malheureusement assez mal les renforts
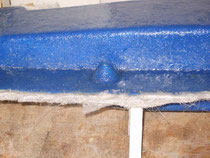
Détail d'un détrompeur . Fait avec un bouton de tiroir en bois . Efficace n'est-il pas
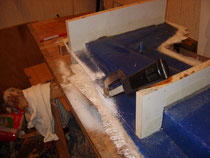
Début du tétourage à la lame de scie à métaux . Je n'ai pas de disqueuse (:o)))
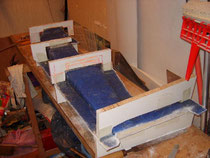
Le même aprés détourage . C'est plus propre .
Le détourage doit se faire avant démoulage .
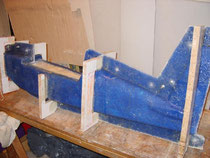
Toujours avant démoulage perçage des trous pour les vis de serrage quand on stratifie les fuselages .
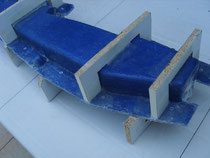
Autre vue avant démoulage.
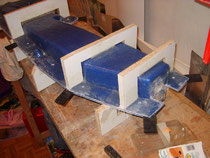
Démoulage en cours . Je le fait avec des cales de pose de parquet flottant .
En noir sur l'image . Elles sont en forme de coin , c'est parfait .
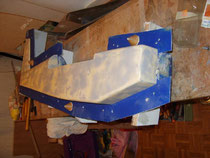
Aprés démoulage de la première partie . Reste à démouler la deuxième partie . En général c'est un peu plus dur mais ça s'est très bien passé . Il faut dire qu'avec 12 couches de cire industrielle ?
On remarque bien les centreurs (cones marons sur les bords ) il y en a 3
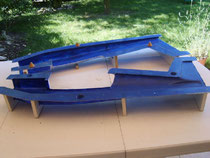
Et en fin 4 mois après le début les deux parties du moule existent .
Reste plus qu'à .
La suite arrive (couples echelle 1 , image des renforts de fuselage : couples train servots..)
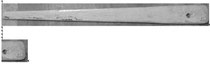
Couple de dérive à l'échelle 1 . Mais attention au programme d'impression et s'assurer que l'imprimante est en paysage.
Le document original et un (.doc) que j'ai du transformer en jpg et donc à l'origine
la zone d'impression n'est pas assez grande . C'est pourquoi il y a deux parties .
Ajuster la superposition des images aprés découpe à l'aide du trou.
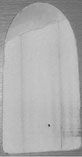
Couple Dossier à l'échelle 1 . Impression en portrait .
Tous ces couples seront à retoucher légèrement en fonction de l'épaisseur du tissus
de stratification . Je pense qu'il vaut mieux tailler un poil plus grand et poncer.
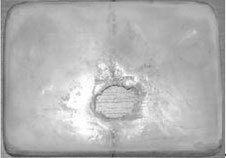
Couple moteur échelle 1 . Idem précédent.
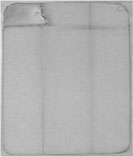
Couple TDB échelle 1 . Idem .
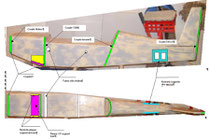
Emplacement des renforts figuré sur le master.
Les dimensions des renforts autres que les couples ne sont pas données car elles sont à ajuster en fonction du matériel utilisé .
Voila c'est fini pour le moment . On reprendra ça lors de la stratification du fuselage et de la fabrication des ailes .
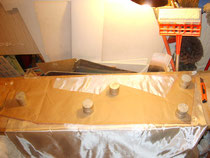
Préparation de la découpe du tissu de verre . Remarquer le patron en papier.
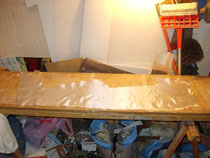
Première couche de tissu découpé . IL faudra un couche de 100g et 2 couches de 160g.
Prévoir que le tissu déborde d'environ 5 cm tout le tour .
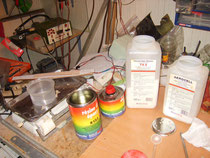
Patériel et produits nécessaires pour la stratification .
Une balance précise au g si possible
De la résine époxie avec son durcisseur de la pour à tyxotroper de l'aérosil et du coton (pour de fibre de verre) et de l'acétone pour netoyer les outils .
Un récipient pour le mélange , une paire de gants en latex , un agitateur (un appui langue vendu en phamacie va très bien) et un pinceau .
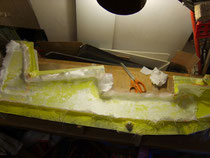
La stratification en cours . Prévoir d'avoir les ciseaux sous la main pour couper le tissu quand il contre tire . Prévoir aussi de mettre un peu de choucroute (résine + aérosil + coton )dans les angles vifs .
Remarquer le masquage du plan de joint avec du scotch à peinture .
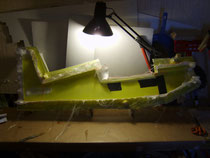
Penser à mettre des renforts aux endroits qui vont subir des contraintes . Si vous n'avez pas de carbone mettre du tissu de verre de 200 ou 250 g .
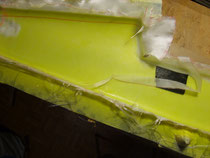
Il est prévu de fermer le fuselage par un bande de fibre de verre tissée sur le plan de joint . Pour que le collage tienne il faut mettre en place une bande de tissu d'arachage (Bande blanche dans le fuselage ) que l'on stratifie tout le long du plan de joint à l'intérieur des deux parties du moule .
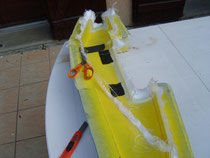
Arrasage du tissu qui dépace du moule . Le gros du tissu est enlevé avec les ciseaux
. Aprés gélification on amèliore l'arrasage au cutter .
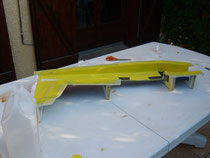
Arrasage terminé
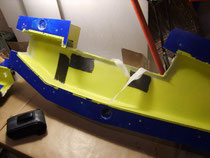
Quand la résine est sèche on envéle le tissu d'arrachage ce qui laisse la surface de collage
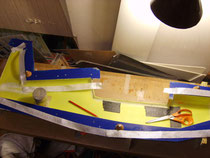
Préparation de la bande de fermeture .
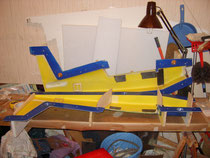
On profite que la résine soit sèche pour ajuster les couples dans le moule
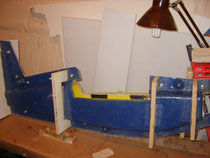
Fermeture du moule par les boulons prévus à cet effet .
A REMARQUER .
Avant la fermeture on dépose un petit cordon de choucroute tout le long du plan de joint (je fais à avec une petite poche de cogélation dont je coupe juste le bout d'un angle pour avoir un petit trou .Type poche de patissier )
Les boulons de fermeture doivent être serrés ferment .
Laiser polymériser au minimum un jour à 20°C ou plus si vous pouvez . Pour certaines résines c'est nettement plus .
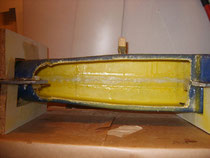
Photo de la bande de fermeture . Penser à l'imprégner avant de la mettre en place et
de résiner la zone de collage avant fermeture du moule .
Les traces blanches que l'on voit sont le surplus du cordon de choucroute qui a débordé à l'intérieur du moule à la fermeture .
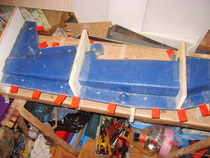
Démoulage aprés séchage toujours avec les câles de pose de parquet flottant
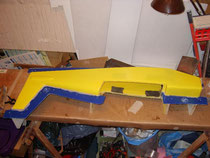
La première partie du moule a été retirée .
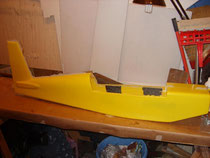
Le fuselage brut de fonderie
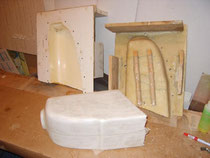
Le capot moteur au sortir du moule et sont moule
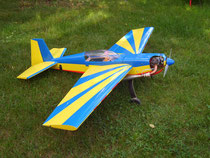
Le résultat final
Mais attention !!!!
Il faut alléger l'arrière au maximum et pas de flèche au stab sinon la punition tombe :
500 G de plomb devant . Il faut même envisager de ramener les servos de profondeur à l'avant .
La fabrication, des ailes n'apas été traitée . Il s'agit d'un noyeau polystiréne découpé au fil chaud coffré balsa et entoilé au Diacov (mais on peut s'en passer c'est plus léger)
Le profil est un EPPLER E474 porté à 16% Corde emplenture 400 mm corde saumon 250 mm longueur 800 mm .
Le stab et la dérive sont un NACA 09 ou 012 sais plus . ???